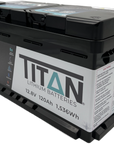
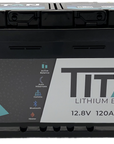
TITAN Lithium 12V 120Ah Battery
Lithium Iron Phosphate: The Safest Lithium Chemistry
Featherweight: Up To 80% Lighter Than Lead-Acid
TITAN BMS Built-In: The World's Most Advanced BMS
Bluetooth Built-In
Smart Charge Heater Installed
Dual Active & Passive Balance
Inverter & Parallel Communications
Compatible With High Performance Inverters
Fully Warrantied For The Battery's Life
Fully Compatible With Victron Products
Product Details
355mm long x 175mm wide x 190mm high
Perfect for those looking for the highest tier of lithium battery for use in camping, marine or renewable storage, our 120Ah lithium is our answer to the standard 110Ah lithium battery from others but packs a bigger punch with a larger capacity, higher quality cells, Bluetooth at no extra cost and an uprated BMS.
This battery is still 190mm tall, so can fit under seats if required, plus can be mounted on its side if you need it 175mm in height.
This battery is also perfect for those who need a 12V power source in a condensed and lightweight package (not for engine starting, though).
TITAN Batteries use Lithium Iron Phosphate cells
TITAN LiFePO4 batteries are inherently safe both chemically and thermally, and do not use rare materials like Cobalt or Nickel. In return, we get a slightly lower cell voltage of 3.2V per cell (4x cells = 12.8V), and a lower energy capacity compared to NMC (Lithium nickel manganese cobalt - the cells used in EVs), however LiFePO4 are much more stable at a chemical level, and have much higher lifespans - our batteries can last between 2,500 and 10,000 cycles (depending on use) - NMC is typically 1,000 to 2,500 cycles.
The omission of Cobalt vastly reduces the chance to start thermal runaway. Many now consider LiFePO4 to be safer than lead-acid thanks to their stability and internal control. They can be used in any orientation (e.g. on its side), although on its base will give the best performance. They contain absolutely no acid, generate no gas emissions and are recyclable.
Massive Cycle Ability
TITAN batteries can be cycled (1 discharge + 1 charge = 1 cycle) between 2,500 to 10,000 times. The amount of cycles corresponds to how deep the discharge is - this is referred to as DOD; Depth of Discharge). If you discharge 100% of the capacity every time you use the battery, it can do this 2,500 times before needing to be replaced. The less capacity used, the higher the cycle life.
In terms of measurable life: if you discharged this battery 100% every day of the year - 2,500 cycles ÷ 365 days = 6.8 years expected lifespan
To put this into perspective, the highest quality lead-acid gel battery (gel has the best cycle count of lead-acid) can do 350-400 cycles at 80% DOD.
Double the Capacity of Lead Acid Batteries
To get the same capacity in lead-acid, you would need two massive, heavy 142Ah batteries (Exide ER650) in a parallel connection to make 284Ah. Just one TITAN 120Ah can save a huge amount of space, weight, extra wiring and has the added benefit of no gassing, so can be placed anywhere.
To compare accurately, we only use Wh (Watt Hour) capacity ratings - Ah (Amp Hour) ratings unfortunately do not take battery chemistry differences into account: TITAN lithium batteries use 100% of their capacity (~90% with Gel, ~75% AGM & ~60% traditional flooded lead-acid). This coupled with lithium's inherent energy density, means our batteries have over double the useable capacity compared to lead-acid batteries.
Ultra Lightweight Lithium - 13Kg
The same capacity in a single lead-acid battery weighs a massive 50Kg (Exide AGM EP1500), and is over twice the physical size. A 37Kg weight saving can mean a huge difference when traveling abroad, as well as offering better MPG on vehicles.
Lithium Prismatic - Class A Automotive Cells
All TITAN lithium batteries use the highest quality lithium cells available. In doing so, we can achieve better performance, higher BMS thresholds and a better overall lifespan compared to others.
We use prismatic lithium cells (they look like a long, thin rectangle) rather than cylindrical cells. Prismatic cells are more expensive and harder to make than cylindrical, but the benefit is a higher quality, higher capacity and potent battery. As all battery cases are squares, our cells fill out all available space within which allows us to boast higher capacities over other brands that use cylindrical cells.
Cylindrical cells can waste a fair amount of internal space as circles put together will always have a gap, and are far harder to repair as they use a lot of spot welding in their design.
What about the cells getting too warm? When discharged at the full BMS allowance, we found all of our batteries to reach a maximum of ~45°C - well within the specification. For lithium to fail, the cell temperature needs to get to around 100°C. As our prismatic cells use aluminium for their outer case, any heat is dispersed with ease. And an added benefit is prismatic is a lot more efficient with heater options - heated options that use cylindrical cells means the internal cells that aren't near the heater mat will not get sufficiently heated and can lead to early failure.
Compatible With Existing Equipment
Our most asked question - can lithium replace your current lead-acid battery? TITAN lithium batteries and BMS is designed as a direct replacement of lead-acid batteries with no need for new equipment. Our custom unique battery cases are designed to be a carbon copy of existing lead acid leisure batteries, meaning users will not need to replace to amend existing battery locations. These battery sizes are known as DIN sizes and are a very common standard across the world.
We do still recommend double-checking your current charging equipment - our batteries are designed to accept AGM or Sealed modes if a lithium/li-ion preset is not available. Look for a maximum charge voltage of 14.4V.
TITAN Lithium batteries are compatible with split charge relays and DC to DC chargers.
For more detailed information, please check out our FAQs.
Our lithium batteries are for running equipment only (i.e. deep cycle use) - they are not designed for engine starting.
TITAN Battery Management System Built-in
It's what's on the inside that counts - all TITAN batteries have their own custom TITAN BMS built-in. A Battery Management System (BMS) is a circuit board that is mounted on top of the internal cells inside the battery which is connected in between the cell terminals, and external battery terminals. The BMS controls and monitors everything with split second accuracy to ensure the battery cannot be damaged when subject to extremes that may otherwise cause cell damage. Many other lithium batteries use an off-the-shelf BMS with pre-set parameters that can skip on vital safety protections - at TITAN, we wanted to push the limits of performance while still managing to ensure safe operation, so we designed our own with the help of industry experts and engineers.
TITAN BMS currently has a market leading 11 protections built-in: over discharge protection, over voltage, under voltage, temperature protection and short circuit protection to name a few, and is designed to provide the highest possible performance, while still maintaining our strict safety protocols.
All protections are temporary and are designed to self-reset or reset when the battery is put on a charger.
TITAN lithium BMS has one of the highest rated BMS current allowances on the market thanks to the use of the best quality materials and internal workmanship.
Matched BMS
TITAN BMS is custom designed by us. Rather than use an off-the-shelf one, we are able to match our BMS parameters to the exact specification of the lithium cell. By doing this, we are able to extract the pinnacle of performance, all while keeping the cell within its safe working window.
We are also able to extract the higher level of our cell quality in the means of extra capacity - all of our batteries can give up to 10% extra capacity than rated once fully charged. E.g. our 120Ah can be 130Ah, 150Ah can be 165Ah, etc. We can't guarantee the extra capacity due to material differences in the cell batches, but our BMS is smart enough to automatically adapt the fully charged capacity, so users can see and make use of any extra capacity via the app.
Cheaper Long Term
Despite its high initial cost, TITAN lithium is cheaper than its lead-acid counter parts over its lifespan. Our design life is 10 years - rounded up this battery costs £600 or £60 a year. The closest capacity equivalent in lead-acid is the Exide AGM EP1500 with a design life of 4 years - currently around £385 or £96 a year (replacing the battery at the 4 year mark). This equates to over £360 in savings at the 10 year mark, plus all the benefits of a lighter, smaller and more efficient battery.
While the design life of TITAN Lithium is 10 years, we expect the average user to reach 15-20 years, making it an even better investment. The realistic average life of Lead-acid is 3-5 years.
Built-in Bluetooth Monitoring
All TITAN Lithium batteries have Bluetooth built-in for live and accurate monitoring. Our app is free of charge, available on both iOS and Android and localised in 10 languages.
When connected, users will be able to monitor the battery in real-time and will see live voltage, current (Amps & Watts), live time calculations - how long till discharged and charged, temperature, Ah capacity, % Capacity (SOC), cell voltages, protection triggers and more.
The TITAN Lithium app is also one of the only BMS apps that can handle multiple connections to multiple batteries in series and or parallel, and will adjust calculations to give accurate monitoring based on your setup.
Heater Installed As Standard
This battery comes installed with an heater mat that surrounds the internal cells, which enables the internals to warm up in freezing conditions. All lithium batteries do not charge when below 0°C in order to protect the cells against damage that may occur - the heater will activate when the internal battery temperature is ~2°C or lower, and there is an incoming charge current to the battery. The heater prioritises it's power source from the charger first, and can take up to 3.6A from the battery if the charger is not powerful enough, and there's enough battery capacity left. The heater will then aim for 10°C, and will switch the incoming charge from the heater to the cells for the perfect charge, whatever the weather.
Battery warm up time will vary on the type of charger and the temperature, but on average, expect an added 20 minutes to your charge time.
The added heater does not affect performance in any way - the battery can and will be able to discharge in -20°C temperatures.
Dual Active & Passive Cell Balance System
All TITAN Lithium batteries come with an active balance system installed. Active balancing is where the internal cells are automatically balanced with each other to ensure all are working equally when discharged and charged by actively monitoring each cell and directing energy to a cell that is lower in voltage than the others, or pulling from a cell that is higher. This system helps avoid overworking a single cell; potentially leading to an early failure.
Passive balance is when the cells are simply connected to each other without actively allocating energy. This method can allow higher voltage differences between the cells and can put more stress on a single cell.
The TITAN BMS is the only BMS on the market that uses both balance methods - passive for small voltage differences, and active for larger. This allows us to keep the BMS energy consumption down, while still benefiting from the full balance suite - the best of both worlds.
- The active balance system is fully automatic and controlled by the BMS
- Active balancing helps keep all cells healthy for longer compared to just passive balancing
- TITAN exclusively uses the most premium quality, batch tracked cells available and intheory, active balancing is not required at this quality level. However as all batteries operate via chemical reaction, tiny material differences can make a difference over time; we include active balancing to ensure the longevity of all TITAN batteries
- Active balancing takes place more often when the battery is charging, and a cell reaches 3.4V
- This is denoted by flashing cells on the battery info tab in the TITAN app
- Balancing takes full effect when the battery is between 90-100% SOC
Automatic & User Hibernation
One of the worst things that can happen to any type of lithium battery is being left in a fully discharged state for a long period. In the worst possible case, the cell voltages self-discharge (~1-2% a month) low enough and can no longer provide power to the BMS, causing it to shut down. If this happens, the BMS can wipe its own memory, causing the entire battery to permanently shut down. TITAN BMS has several built-in backups in place, but will require the battery to be returned to us for recovery. To help avoid this issue altogether, we've developed the hibernation function.
All TITAN Lithium batteries come with two hibernation functions - automatic and user controlled. Each function will shut down various active parts of the BMS to help keep the battery self-discharge rate as low as possible while the battery is not in active use.
Automatic hibernation will activate when the battery is at a low state of charge and has been inactive for a few days. When active, the battery will not output a voltage or current and will have enough capacity to last around 6 months (longer with larger batteries) before reaching a critical level. This allows users more time to notice and recharge; preventing any cell damage at the same time - essentially adding a low voltage safety net.
User controlled hibernation is triggered by the included on/off cable. This function switches the BMS charge and discharge functions off and on; the BMS stays active, but will not allow any charging or discharging to take place. This is intended for when the battery is connected to a vehicle going into storage and power to devices is not required for the storage period - all electrical devices will still take some energy, even when switched off. This function stops devices from slowly draining the battery over time.
When in automatic hibernation, this function is designed to be easily switched off by placing the battery on charge, or by connecting to it via the TITAN Lithium app.
Data Communications (comms)
All TITAN Lithium batteries have communication (comms) ports built into either the top or side of the battery case. These ports are for users who are connecting single or multiple (parallel) batteries to a compatible data-enabled inverter or device.
Compatible With Popular Inverters & Devices Using CANBUS, RS485 & NEMA2000
Connecting to an inverter allows the parameters and live BMS data to be pushed to the inverter or compatible device for a more efficient setup; it will sync and pre-set alarms, low voltage cutoffs, discharge and charge settings, and if using compatible software, can be monitored remotely e.g. using Victron VRM.
Depending on the brand/data protocol, special cables are required for data communication - all cable types are available from TITAN Lithium.
By default, TITAN BMS is pre-set for use with Victron CANBUS via VE.CAN and BMS.CAN ports. TITAN is compatible with Victron's DVCC mode.
The data mode can be changed on request to another brand/protocol, but can only be done by TITAN engineers; leave us a note at the checkout if you need us to change the data mode before delivery.
TITAN BMS has known compatibility with:
- Victron GX devices (default) - CAN
- Growatt - CAN
- Sacolar - CAN
- Goodwe - CAN
- Voltronic Power - RS485
- Sofar - CAN
- Sorotec - CAN or RS485
- Deye / SunSynk - CAN or RS485
- Solis - CAN
- Luxpower - CAN
- Pylon Tech - CAN or RS485
- Sol-Ark - CAN
- SRNE - RS485
- MUST - CAN
- SMA - CAN
- MEGAREVO - CAN
- MPP Sola - RS485
- TBB Power - CAN
- Senergy - CAN
- Schneider Electric - CAN
- Aiswei - CAN
- SMK - RS485
- Foxess - CAN
- SunGrow - CAN
Compatible With High Powered Inverters, Pumps & Motors
Some high performance inverters, pumps and motors can require a very high current for a split second on start-up; this is called an inrush current and usually happens if the device has large copper windings and/or capacitors. At 12V, some devices can easily peak up to 1,500A for a microsecond.
Many lithium battery BMS's can struggle with this as they see the high current and view it as a short-circuit, so will trigger their protection and shut the battery down. TITAN BMS has been developed to safely allow high start up currents without triggering a protection too early, making it an ideal match for high performance systems and machines.
High-Performance Dual Connection Copper Round (SAE/Automotive Terminals) & M8 Terminals
Perfect as a drop-in replacement for lead-acid batteries, our high-performance copper terminals ensure the best electrical performance while inherently providing corrosion-free contact, and now includes a M8 integrated nut and bolt connection for universal fitment without the need for adapters.
Electrically Efficient
Thanks to our 99% efficiency rating, TITAN batteries utilises incoming charge energy with little waste; making them a perfect partner for solar chargers. Our batteries can accept extremely high charging amps which means they can be charged extremely quickly - from 0% to 95% in less than 2 hours (when charged over 100Amps).
This efficient charging means TITAN batteries are also perfect for home solar storage (although we'd recommend looking at our higher voltage batteries for better BMS efficiency).
A Market First - Lifetime Warranty On All Batteries
At TITAN, we are so confident in our build and component quality, we have upgraded all of our batteries that have grade A cells to our full warranty that lasts the lifetime of the battery. Our parent company celebrated its 75th anniversary of continuous business this year, and we plan to stick around for the foreseeable so you can rest easy that we will be here for any issues that may arise; be it tomorrow, or in 10 or even 30 years.
Important to note: like anything in life, the more you use something, the more it wears out - batteries have always been the same, and their capacity will degrade over time. This reduction is normal and to be expected; the harder you use the battery (i.e. you discharge it fully and charge it fully often), the faster its fully charged capacity will decrease. Lithium has an incredible resiliency to capacity reduction though, and we expect a capacity loss of about 5-10% every decade with normal use and charging within specifications e.g. a brand new 150Ah would have a fully charged capacity of 165Ah, a 10 year old 150Ah would have ~150Ah and a 20 year old 150Ah would have ~135Ah when fully charged.
Battery wear or capacity loss are not valid warranty claims. Once a battery reaches a fully charged point and it does not last very long or last as long as you need it to, you will need to replace the unit.
Our warranty covers all components against premature failures caused by manufacturing faults. For more information on our warranty terms, please click here
Our Batteries are Repairable
If anything does fail prematurely, we aim to repair or replace individual problem components rather than replace the whole battery. Doing this also allows us to reduce our carbon impact and reduce waste. As we are a family of battery specialists (we used to make batteries in the 1950s), we are adept at any and all repairs should they arise.
Technical Specs
ELECTRICAL SPECIFICATIONS | |
---|---|
Nominal Voltage: The battery's working voltage
|
|
Capacity: |
|
Energy: Watt-hours is our recommended capacity to use when comparing against other battery chemistries
|
|
Resistance: |
|
Efficiency: How efficient current is used without loss to resistance and heat
|
|
Self Discharge: The standby self-discharge amount without use - all batteries have some level of self-discharge but lithium has one of the lowest
|
|
PHYSICAL SPECIFICATIONS | |
Dimensions: |
|
Weight: |
|
Terminal Type: |
|
Case Material: |
|
Enclosure Rating: While resistant to water ingress, all batteries should avoid water where possible
|
|
Cell Chemistry: |
|
Cell Type: Lithium batteries can either be made with cylindrical or prismatic cells - cylindrical is cheaper and easier to make while prismatic is more efficient with space so can offer larger capacities
|
|
TITAN BMS SPECIFICATIONS | |
Consistent Discharge: Maximum amount of amps you can pull from this battery for an unlimited time (until it goes flat)
|
|
Peak Discharge: The absolute maximum amount of amps this battery can output over the consistent discharge rating for a period of time
|
|
Maximum Charge Rate: |
|
Low Voltage Charge: Battery nearing 0% - charge at this voltage
|
|
Low Voltage Disconnect: The battery will switch off discharging at this voltage. The battery will need to be charged ASAP at this point
|
|
Short Circuit Protection: This protection triggers should a short circuit occur. We use a maximum amp rating and how fast it triggers (the faster the better)
|
|
Recommended Charge Rate: Based on average consumer charge ratings and time to charge
|
|
Recommended Charge Voltage: |
|
Maximum Charge Voltage: |
|
Maximum Connections: |
|
Discharge Temperature Range: |
|
Charge Temperature Range: |
|
HEATER SPECIFICATIONS | |
Heater Activation: |
|
Heater Power Source: |
|
Heater Target: |
|
Heater Consumption: |
|
CELL BALANCING SPECIFICATIONS | |
Cell Balance Method: |
|
Active Balance Activation: |
|
Passive Balance Activation: |
|
COMMUNICATION SPECIFICATIONS | |
Default Set Protocol: |
|
Victron DVCC Compatible: |
|
Other Compatible Protocols: |
|
Battery Parallel Communication Via: |
|
In The Box | |
Included: |
|
Downloads | |
Safety & Compliance | |
|
|
|
|
|
|
|
|
|
|
|
|
|
|
|